Understanding the Basics of Plastic Injection Molding Processes
Plastic shot molding serves as a foundation of modern manufacturing, offering a methodical approach to generating intricate parts with precision. Exploring these crucial elements can expose exactly how even small changes can lead to considerable enhancements in production outcomes, increasing questions about the possibility for development in this well established process.
What Is Plastic Shot Molding?
Plastic shot molding is a widely used manufacturing procedure that transforms thermosetting and polycarbonate products right into exact and complex shapes. This technique is preferred for its capability to generate high volumes of the same parts with exceptional precision, making it an important method in different sectors, consisting of vehicle, customer items, and medical devices.
The process entails melting the picked plastic material and injecting it into a mold and mildew under high pressure. The mold, made to the specs of the wanted part, allows the molten plastic to form as it cools and strengthens. As soon as the material has solidified, the mold is opened up, and the ended up component is ejected.
Plastic shot molding supplies several advantages, including minimized waste, consistency in production, and the ability to integrate elaborate layouts that might be testing with various other making methods. In addition, it sustains a wide range of materials, each providing distinct buildings that can be tailored for specific applications. As industries remain to innovate, plastic injection molding stays at the leading edge, allowing the advancement of innovative items that meet advancing consumer demands.
The Shot Molding Process
The shot molding process is an advanced technique that entails numerous vital phases to create premium plastic elements. Initially, plastic pellets are fed into a warmed barrel where they are melted into a viscous fluid. This molten plastic is after that injected under high stress right into a precision-engineered mold and mildew, which forms the product into the wanted form.
Once the mold is loaded, the plastic is enabled to solidify and cool down, taking the form of the mold cavity. Air conditioning time is critical, as it affects the cycle time and the final residential or commercial properties of the shaped component. After enough cooling, the mold and mildew opens, and the finished component is expelled utilizing ejector pins.
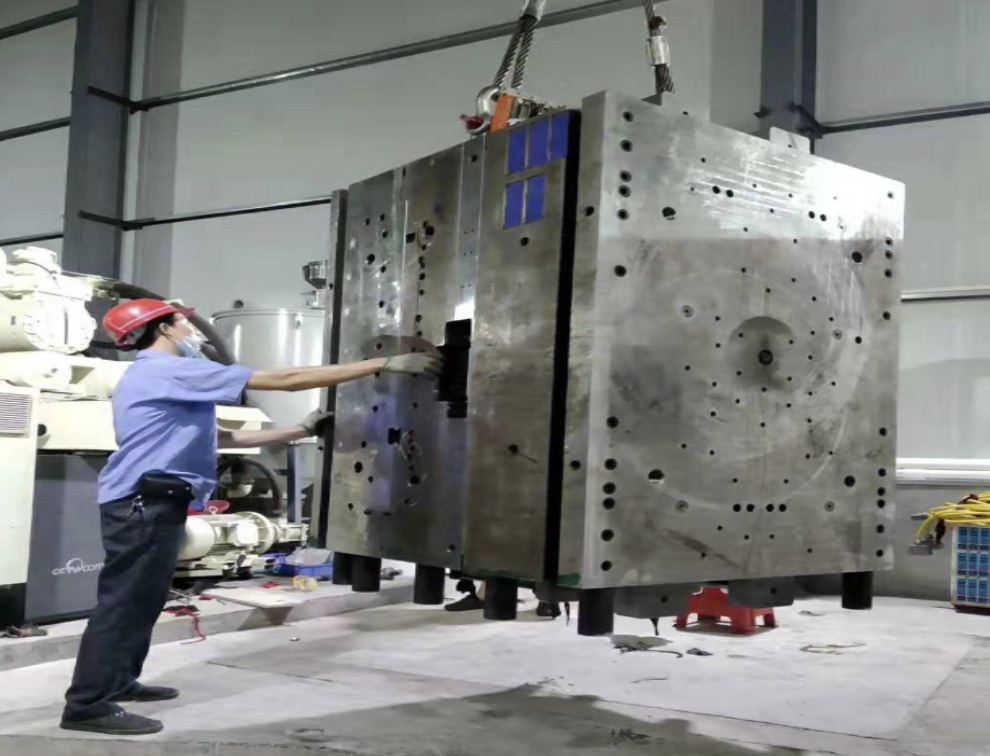
Materials Made Use Of in Injection Molding
Various materials can be utilized in the injection molding process, each offering special properties that cater to certain applications. One of the most generally made use of products include thermoplastics, thermosetting plastics, and elastomers.
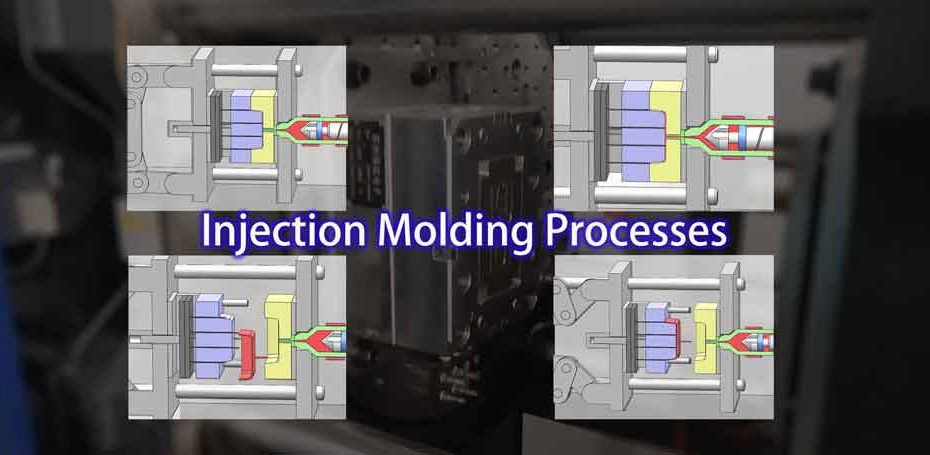
Thermosetting plastics, like epoxy and phenolic materials, go through a chemical change during the curing process, leading to an inflexible, inflexible structure. These products are excellent for applications needing high heat resistance and structural honesty, usually utilized in automobile components and electric insulators.
Elastomers, consisting of silicone and rubber-based materials, provide flexibility and strength. Their distinct residential or commercial properties make them ideal for applications that demand flexibility, such as gaskets and seals.
In addition, specialty materials like bio-based plastics and compounds are gaining grip for their why not look here ecological benefits and enhanced efficiency qualities, widening the range of shot molding applications in numerous industries. Recognizing the residential or commercial properties of these products is critical for choosing the ideal kind for details tasks.
Benefits of Shot Molding
Injection molding attracts attention as an extremely effective production process that uses various advantages for creating complicated parts with precision. Among one of the most considerable advantages is the capacity to produce intricate styles that would certainly be tough or difficult to accomplish with various other methods (Plastic Injection Molding). The process enables comprehensive features and tight resistances, making sure top notch elements
Additionally, injection molding is understood for its quick production capacities, making it a suitable choice for high-volume manufacturing. Once the mold is created, components can be generated rapidly, minimizing lead times and raising total efficiency. This efficiency browse around this web-site not just decreases manufacturing prices however also gives an one-upmanship in the marketplace.
The convenience of products utilized in injection molding further boosts its allure. A wide variety of thermoplastics and thermosetting polymers can be utilized, allowing suppliers to pick products that best meet their specific demands, including stamina, adaptability, and warmth resistance.
Furthermore, the procedure lessens waste, as excess material can typically be recycled and reused. This sustainability element adds to a lowered environmental effect, making injection molding a liable manufacturing option. Overall, the benefits of injection molding make it a preferred approach for several markets.
Variables Impacting Item Top Quality
While various elements can influence product high quality in shot molding, recognizing these aspects is vital for attaining optimum results. Secret elements consist of material choice, refining specifications, and mold layout.
Product selection plays a crucial duty, as different polymers exhibit one-of-a-kind properties that influence flowability, stamina, and thermal security. Insufficient material choice can result in problems such as warping or insufficient filling.
Processing specifications, including cycle, temperature, and stress time, should be meticulously regulated. Variations in these settings can result in disparities partly dimensions and surface area finish. As an example, excessively heats might trigger deterioration of the polymer, while poor stress can result in short shots.
Mold and mildew design is equally essential, as it figures out the circulation of the molten plastic and the cooling read this process. Badly developed mold and mildews might lead to irregular cooling rates, causing dimensional errors and recurring tensions.
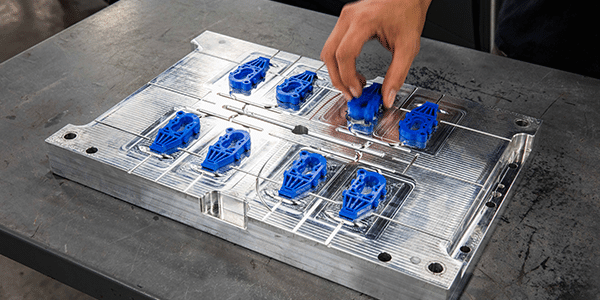
Conclusion
Finally, plastic shot molding acts as a critical production procedure that makes it possible for the effective manufacturing of top notch elements. Mastery of the shot molding procedure, consisting of the understanding of products and the influence of various elements on product quality, is essential for achieving optimal results. The benefits of this approach, such as cost-effectiveness and style flexibility, further underscore its significance throughout several industries, solidifying its status as a recommended option for high-volume manufacturing.
Plastic shot molding serves as a foundation of modern-day manufacturing, offering a methodical technique to generating complicated components with accuracy.Plastic injection molding supplies numerous advantages, consisting of minimized waste, uniformity in manufacturing, and the ability to include complex designs that might be challenging with various other producing approaches (Plastic Injection Molding). As industries continue to introduce, plastic injection molding stays at the forefront, enabling the development of sophisticated products that satisfy evolving consumer demands
The shot molding process is an advanced method that involves numerous key phases to create top notch plastic components.In final thought, plastic shot molding serves as a vital manufacturing process that makes it possible for the efficient production of high-grade elements.